How manufacturers can eliminate the stress of frequent change
Think of a house of cards. Each piece that you add to the tower plays an extremely important role in supporting the others, but the failure of one always leads to a total collapse. You can view suppliers and their relationship with manufacturing partners in a very similar way.
Suppliers play a major role in the supply chain for manufacturers, providing raw materials and different components necessary for manufacturing. However, there are plenty of challenges that can arise, often affecting their supply chain partners in a detrimental way. When these challenges arise—oops! The house of cards topples, and manufacturers don’t have what they need to make and send out their products on time.
Manufacturers depend on their suppliers’ stability, but frequent changes are the culprit of manufacturing obstacles. Luckily, there are easy ways to identify and mitigate these risks before they become overwhelming.
What’s driving frequent changes
When one supplier can’t hold up their end of the agreement, all other supply chain partners are impacted as the order changes to accommodate adjustments.
There are always changes in the supply chain that are expected, including weather-related issues or global import/export delays that slow down order fulfillment. However, there are several trends that drive increased risk for changes that affect supply chain stability.
Some factors that have increased frequent changes in the supply chain are:
COVID-19: Since 2020, the pandemic has had cascading effects on global supply chains and material availability. Whether it’s a personnel shortage or delayed freight lines, the effect of COVID-19 is still creating obstacles in the supply chain.
Geopolitical conflicts: Conflict creates disruptions that trickle down, affecting material sourcing and transportation routes.
Rapid inflation: As inflation rises, supplier costs and raw material prices increase. Some supply chain partners may need to make decisions that affect their partners upstream or downstream, such as halting production or changing the product materials.
Vendor diversification and collaboration are critical
How can we combat the negative effects of frequent supply chain changes? Vendor diversification and stronger partner collaboration are the answer.
The risk of supply chain changes is simply too important to ignore; if you’re missing a crucial manufacturing component, you can’t produce. Spend time investing in your suppliers to ensure you’re working with reliable, trustworthy partners.
It’s also crucial to diversify your vendors to have effective risk management practices. This way, if one supplier fails, you have a backup option. It can be tempting to wait until you need a new vendor, but by having another one on hand, you’ll have options when you’re missing a critical material for production, saving you the hassle of delays (and not to mention, a lot of money).
Spreading business across multiple suppliers helps manufacturers:
- Minimize reliance on any single source.
- Enhance supply chain resilience to better withstand unforeseen challenges.
- Reduce vulnerability to disruptions.
Strategies for supply chain disruption mitigation
The key to mitigating supply chain disruptions and frequent changes is agility. Being agile in your supply chain processes means you always leave yourself with plenty of options when an alternative solution is needed. Some strategies for agility:
- Regular assessment and expansion of your supplier base.
- Implementation of vendor quality measures and monitoring systems.
- Establishment of contingency plans for quick adaptation to supplier changes.
Additional steps manufacturers can take to enhance supplier collaboration:
Improve your data transparency and timely communication
Enhance visibility into orders and inventory. Leverage technology that can provide real-time data to better communicate with your suppliers and ensure everyone is on the same page. More transparency can also help identify potential issues faster, and you can address them before they escalate into larger problems.
Effective communication channels significantly reduce delays that are caused by misunderstandings or a lack of information.
Automate procurement processes
Automated procurement processes help you avoid reliance on manual methods like paper, email and phone-based updates, which are manual and time-consuming. By introducing automation, you can save time while avoiding delays and errors.
Automated systems ensure that order updates and inventory levels are promptly communicated, allowing faster and more accurate decision-making. Automation can also play a huge role in invoice entry and reconciliation.
Alleviate the stress of frequent changes
It’s a good time to evaluate your existing processes and learn how you can improve your agility and collaboration to strengthen your supply chain. Prioritize vendor diversification and automated procurement to boost your confidence in disruption preparedness. Remember: a resilient supply chain is the key to success.
To learn more about how to be prepared for anything in today’s volatile landscape, dive into the Manufacturing Supply Chain solution from SPS Commerce.
- A comprehensive overview of manufacturing business problems - November 19, 2024
- The importance of effective demand planning - November 19, 2024
- How manufacturers can eliminate the stress of frequent change - November 19, 2024
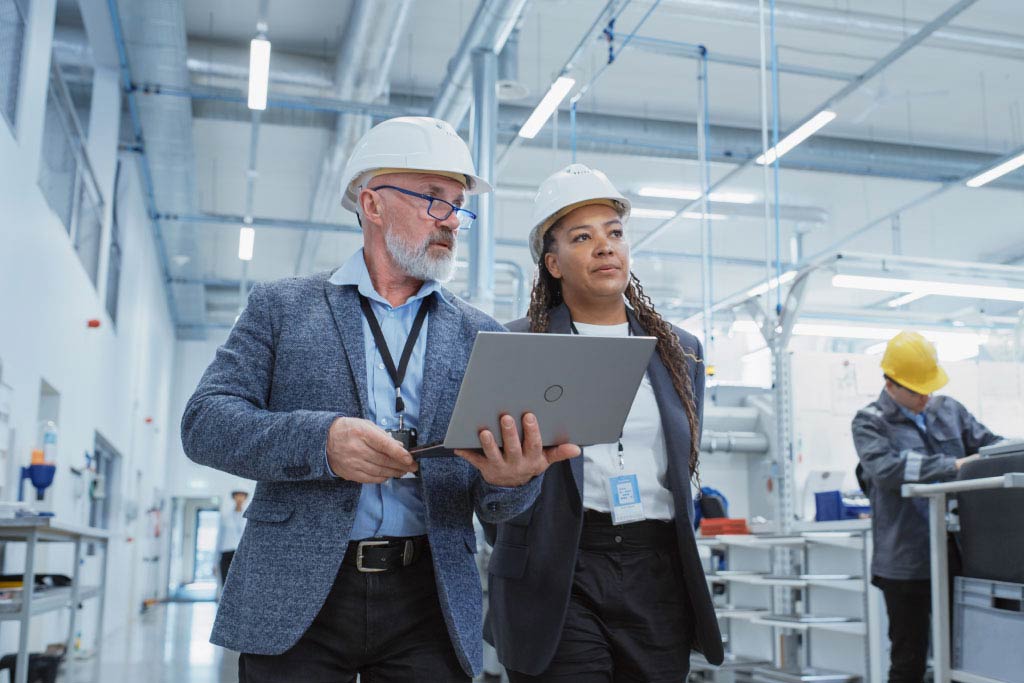
RELATED POSTS
What is a 2D barcode and how does it ...
Seeing clearly in a complex market
Retail data is your true north in a s...